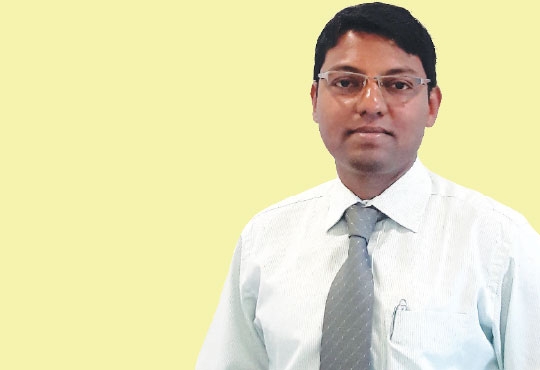
Requirements for Precision CNC Parts Machining
Megha Jain, content writer | Friday, 13 October 2023, 04:27 IST
The world of manufacturing is seeing unprecedented levels of precision, thanks to advancements in CNC machining. With CNC machines constituting a market size of around $95 billion in 2022, the industry is continuously evolving with innovations that aim to serve players in the market with better accuracy, speed, and repeatability.
However, achieving precision in CNC parts goes beyond just the machine. Let's delve into the primary factors that are crucial in ensuring the highest precision in CNC machining.
The Precision Journey Begins With Prototyping
Before delving into the intricate requirements of precision CNC part machining, the spotlight must shine on the initial phase: rapid prototyping. Reliable rapid prototyping companies, such as 3ERP, set the foundation for the machining process. Therefore, if you're looking to source your rapid prototypes and custom parts with precision and efficiency, be sure to visit https://www.3erp.com/ to learn more about them.
They leverage the latest CNC technologies and expert knowledge to ensure that your prototype is as close to the final product as possible, giving you confidence in the design and functionality of your parts. As the prototyping phase often dictates the success of subsequent manufacturing stages, it's clear that precision begins right from the outset.
Selection of Raw Materials
Choosing the right raw material forms the basis of precision CNC machining. The material selected will determine how the part behaves during the machining process and its final attributes.
For example, the hardness of the material can influence the type of cutting tools required, while its grain structure might impact the finish of the part. Potential deformities in materials can also lead to imperfections in the final product. As a result, a keen eye for quality control is indispensable during material selection to ensure the material's suitability for the intended application.
Integrated CNC Machinery and Tooling Strategy
Precision CNC machining depends heavily on the combination of the machinery used and the tools and strategies adopted. As CNC machine tools evolve, they increasingly address the demand for precision.
Essential machine features, such as spindle accuracy, play an important role in determining how precisely a machine can trace a toolpath. Moreover, the rigidity of a machine ensures stability, warding off vibrations that could compromise precision. Thermal stability in machinery prevents parts from expanding or contracting during prolonged operations, which could introduce errors. Maintenance and calibration are also crucial for machines to produce parts consistently within tight tolerances.
The tooling aspect cannot be overlooked either. The market is rich with a variety of cutting tools tailored for specific operations, such as drills, end mills, and turning tools. The geometry and coatings of these tools can dramatically influence the precision of the cut. Modern toolpath strategies, like adaptive clearing and high-speed machining, further enhance CNC machining's accuracy and surface finish. Ensuring synergy between the machinery's capabilities and the selected tools and strategies is essential for achieving precision.
Quality Control and Measurement
Ensuring precision in CNC parts requires a rigorous quality control mechanism. This is where advanced measuring tools come into play. Coordinate measuring machines, for instance, provide detailed 3D inspections of parts to ensure they meet the desired specifications.
Laser scanners can quickly and accurately gauge the dimensions of complex parts, while touch probes can measure the insides of features like holes or slots with high precision. The calibration of these tools and regular inspections are very important. They ensure any deviations are caught early and repeatability is maintained throughout the machining process.
Operator Skill and Training
While machines, tools, and materials play significant roles, you can't underestimate the human element in precision CNC machining. An expertly trained operator can not only run the machine efficiently but also recognize potential issues before they become major problems.
Continuous training ensures operators stay informed of the latest techniques and best practices. Their expertise often acts as the final line of quality control, ensuring that parts coming off the machine are of the highest standard.
Environmental Factors and Workshop Conditions
The environment in which CNC machines operate can profoundly impact their precision. Even slight temperature fluctuations can cause materials to expand or contract, throwing off measurements by critical micrometers. As such, many high-precision workshops are temperature-stabilized. They also ensure condi- tions are dust-free, minimizing the risk of foreign particles interfering with the machining process.
Additionally, controlling vibrations is crucial. A stable machine foundation and strategic workshop location can prevent external vibrations, such as those from heavy machinery or passing vehicles, from influencing the CNC machine's operations.
Conclusion
Precision in CNC part machining is a group of various elements delicately working together. From the material used to the machines, tools, and even the operator's skill, every aspect has its part to play. Investing in the right technology, ensuring rigorous quality control, and continuously upskilling operators are all paramount for anyone aiming for the pinnacle of precision in CNC machining. As the industry continues to evolve, staying informed and proactive in adopting best practices will remain the keys to achieving and maintaining precision.
CIO Viewpoint
Some Other Aspect of Solution Selection
By Shiv Shankar Datta, Head IT, FCA Fiat Chrysler Automobiles
Technology - The World of Iron and Steel
By Ashok Kumar, CTO,Tata Steel
Top 5 Must-Haves to Make Smart City a Success...
By Ankush Tiwari, CTO, Mobiliya Technologies
CXO Insights
Design as a Service: Done Right
By By Debprotim Roy, Founder & CEO, Canvs
Engineering Discipline is Catalytic for Overall...
By Pradeep Vajram, CEO, SmartPlay Technologies
Should a CIO Invest in Product Development?